Is it Worth Buying a “Pro” Model Saxophone? – Part I
This article is part one of a two-part interview series with Matt Stohrer on what it is that makes a saxophone a true “pro” model.
With his relentless passion for all things saxophone, Matt Stohrer is a fountainhead of in-depth knowledge when it comes to the repairing, selling, and trading of saxophones.
After servicing some of New York’s best and brightest saxophone stars with his repair and sales outfit in New York City, Matt opted for a slower and more serene way of life in North Carolina, where he continues running a successful business and further mastering his craft.
In this special interview, Matt shares his insights on the mysterious topic of what makes a saxophone a true “pro” model and what you get for the extra dollars you’ll be shelling out to buy a product labeled as “professional.”
The Interview
Doron Orenstein: When it comes to the new horns being built these days, generally speaking, do you believe that for most people, the pro horns are going to actually sound better than the student horns, or is this simply a case of marketing?
Matthew Stohrer: It completely depends.
Say we have a perfect selection of student horns of good quality along with professional horns of good quality. In this case, the student horns will be almost as good as the professional horns, probably so much so that there will be a few people who choose as a matter of taste the student horn over the professional one. These people will be in the minority, but the reason behind this is that a well-built student horn should be almost as good! However, this is not often the actual choice before the consumer.
Let’s see why.
A perfect example of a good “student” horn is the original Bundy. The story goes like this: Buescher Band Instrument Company was a company in the USA who made professional saxophones, among them the Buescher Aristocrat in the 1930s, which was used by famed alto sax player Johnny Hodges.
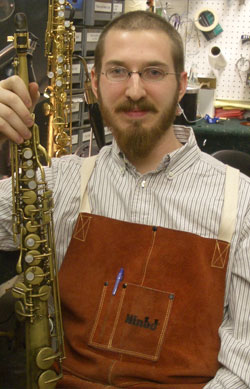
Later on in the 60s, Buescher was bought out by Selmer USA, who took the tooling for the Buescher Aristocrat, cheapened the design a bit, and called it a Bundy. The Bundy I (not the Bundy II) is basically a slightly cheapened professional horn! They have the same bore, the same neck, almost the same keywork, made in the same factory under a new name, and when in proper working shape, basically the same beautiful tone.
This horn will sound excellent, and its only limitation is its label! But unfortunately, this instrument is not made anymore. Another example of this type is the Martin Indiana – also an extremely well-built horn that plays great – and is also not made anymore.
A perfect example of a bad “student” horn is a hypothetical saxophone, one which I will not name, but I will tell you how it was made.
“Eastern Horn Co.” in East Asia decides they want to sell a cheap saxophone. They hire local labor, many of whom have never played saxophone, and train them each to carry out specific parts of the saxophone manufacturing process over and over and over. They buy a modern Yamaha, and they take measurements, copying the instrument. They do a fairly decent job on the surface, but many things are overlooked. In the end, a saxophone is made that plays ok, looks very much like a nice saxophone, but has many foundational issues with regards to its construction – from its internal bore to its mechanism – that are ill-made, built with cheap materials, or perhaps even made incorrectly from the start.
Several examples of this instrument are constructed as well as the factory can manage and taken to a trade show. At the trade show, a well-known US company which we’ll refer to here as “Music Business People Ltd.” sees the saxophone, likes it, and decides to have Eastern Horn Co. build them a large number of saxophones.
Quantities and options are ordered, and Music Business People Ltd. sends Eastern Horn Co. its logo and artwork to be stitched on the case and engraved on the saxophone. Then, when the saxophone is being built by Eastern Horn Co., the saxophone is then engraved “Music Business People Ltd.” (called “stenciling”), which in this case happens to be a well-known brand. The horns are shipped to the US and sold by Music Business People Ltd. for close to $1,000 . Its brand and its price combine to make the purchaser think the instrument is a good instrument, when in fact it has built-in weaknesses and errors in construction and will probably only last a few years before it breaks down or becomes so troublesome to play that the student quits.
This horn is made today, and unfortunately in recent years this type of instrument has become the status quo for student instruments. These instruments can be found at all price points, from the aforementioned example to the $250 eBay specials. Some of them are so bad, that many repairmen will not even work on them. This horn is limited from day one, and it is quite unlikely to sound as good as a properly made saxophone.
I have, in fact, seen this part of the industry first-hand, as I was a “consultant” to a saxophone factory in East Asia (where I recommended many changes, some of which percolated into a large segment of the student market in the past couple of years). Some of what they made was surprisingly good, some of it surprisingly bad, with basic errors in design being carried through to the finished product and shipped and sold across the world. This was years ago, and it was an eye-opening experience for me on many levels.
In fact, many of the student saxophones out there today come from about a dozen of the most prolific factories, and many “brands” you see stateside are in fact the same horn, just with different engraving.
Unfortunately, marketing combined with a majority of consumers who are uneducated (through no fault of their own, as information on this subject is limited, hence my long-winded responses) about saxophones make for a market that is at best difficult to navigate and at worst ripe for hyperbole and sometimes outright lies.
There are dozens of student saxophones that are simply garbage – I wouldn’t play them if they were given to me. Most of the time these are the cheapest of the cheap models and can be avoided simply by avoiding unknown brands at extremely low prices.
Other times, horns are marketed as professional, given a gold plating, and sold as “designed by xxxx”, and consciously portrayed as better than they are. I have had the unhappy experience several times of informing someone that the $2,000 “pro horn” they bought is in fact a student model and suffers from many built-in flaws and limitations that would be very costly to fix.
How can the consumer avoid such an experience? By doing business with honest people who will tell you the origins of their instrument, or sticking with a known manufacturer. Notice I didn’t say brand!
For a peek behind the curtain of this part of the industry and to see what we repairmen see when we service a poorly made instrument, read my friend Curt Altarac’s article Turning a Cheap Imported Instrument into a Finely Crafted Machine.
For my take on why there exists so much mediocrity in consumer goods and services, read The Unprofitable Valley or: Why So Much Stuff Is Mediocre. [Sorry(!), but this web page has disappeared since the original publication of this article]
To read part two in this series, hop on over here.
For more information on his repair services as well as saxophone sales, see Matthew’s website at StohrerMusic.com.
Photo by Martin Barland
August 22, 2011 @ 4:10 pm
Matt is hands down one of the finest repairman out there, and definitely somebody of rare integrity. Thanks for sharing these insights. There’s definitely more than meets the eye to these horns, and sending a student out to buy a new horn is not so simple these days. Everybody should really do their research, and make sure somebody that plays gives anything a try before buying it!
August 22, 2011 @ 9:05 pm
Whoa, cool that you know Matt! Although I haven’t had the pleasure of having him work on one of my horns, I can definitely agree about the integrity and in depth knowledge he has. Glad you dug the article. :-)
September 22, 2011 @ 9:21 am
Thanks, Sam! I’m glad you enjoyed the article, and I hope your horns are holding up well.
Is it Worth Buying a “Pro” Model Saxophone? – Part II | Best. Saxophone. Website. Ever.
August 29, 2011 @ 6:03 am
[…] If you haven’t done so already, check out part I to get the full scoop. […]
Is it Worth Buying a “Pro” Model Horne : Reeds.
May 23, 2012 @ 6:36 am
[…] If you haven’t done so already, check out part I to get the full scoop. […]
Stohrer Music News, Vol. 2 « News « Stohrer Music
May 15, 2013 @ 9:18 am
[…] did an interview for a sax website a while back, it got such a positive response I now have a repair column, for […]
January 26, 2016 @ 10:18 pm
When I entered 5th grade in the Bronx, NY.. I was given a choice of instruments to learn. I suppose I was deemed “musically inclined” by how I handled learning the “song flute” in the 4th grade. In actuality I had already been playing Hazel Scott’s “Boogie Woogie” on the piano, grandma-taught. I digress, I was leaning towards either the Trombone or the Saxophone; Bobby Colomby suggested I take up the Drums, Dick Halligan pushed Trombone and Fred Lipsius who happened to be dads childhood and life best friend won the “suggest” contest and I took up Alto Saxophone. Fred went with me to 48th St in NYC to help me pick out a saxophone. Fred played Beuscher and as such I also played Beuscher. This was 1968 and Blood Sweat & Tears was just embarking on their worldwide tour. The entire group of BS&Ters sometimes “jammed” in our Bronx apartment, I know that sounds pretty far-fetched, but.. hey, what can I say? they did. We “held” Freds baby-grand piano while he was on tour. I digress again;
.
I took private sax lessons from Bill Sheiner, and I didn’t like these lessons, Bill was a strict teacher, and often poked me in my chin with a sharp pencil to enforce my embouchure. I loved playing the sax. I STILL love playing the sax, been in several funk bands over the years, and don’t remember what happened to that Beuscher horn. Since the advent of the internet I have been able to “measure” my “sound” and I don’t like it. I called Fred Lipsius 2 years ago and asked if i could have one of his mouthpieces and he sent me one of his Meyer 5 pieces, and talked my ear off in the process; anyone that knows Fred will agree that you need to have several hours free when you call Fred.
.
I have a Conn alto sax.. it sucks and everything I play sounds like toooot, toooot, toooot, instead of braaaaa, braaaaa, braaaaaa. I’m stuck and don’t know what to do. I can’t afford $2000 to buy a horn. I’m hearing people playing (on Youtube) who’ve been playing for less than 10 years, and they sound much better than I, who’ve been playing since 1968..
.
I need help in finding an affordable Alto as well as an affordable Tenor sax.
June 22, 2016 @ 12:48 pm
Matt: What is your honest opinion of the Big Bell Pro Level Cannonball Raven tenors and altos? I have a Selmer Mk VI tenor and a student model alto. Looking for a backup tenor and a pro alto. I played the Keilwerth SX90’s when I was in NYC but I cannot afford them. Thanks. Btw- I bought my MK VI tenor new in 1974. I saved up almost 2 yrs to be able to buy it while I was in high school. I have a 60’s vintage metal Link 8* that I bought for a song before ebay and the internet. The same for my Meyers 70’s alto mpc.
February 28, 2018 @ 8:24 pm
Not Matt but can put in my 2 Cents as I just Purchased a Cannonball Raven Big Bell Stone series . I’ve played professionally 35 years taught even done some stretches in the repair business . I’ve played and collected every well respected brand of sax . I’ve played my main Ax a Selmer Mark VI Tenor I hand picked from 6 already hand selected tenors. I never thought I top my beloved Selmer tenors sound as well as feel . Last month I was killing time at a music store in Atlanta . I tried a Cannonball Tenor out just to kill time. I was literally blown away in Every way ! Went back ( Long drive) the next week just to be sure my mind wasn’t playing tricks on me and I took my Selmer . Side by side there was no contest the Cannonball “ Kilked It “ all around . I purchased it on the spot ! The most amazing horn I have ever played or heard hands down .
April 1, 2019 @ 5:54 pm
I have an H. Couf Professional Alto Sax, by Julius Kielworth, that I bought from a friend for $500 in the late 1980’s . It was previously owned by my Sax teacher. I also still have my student model Yamaha YAS-23 Alto Sax from 1980. I have to say that the Yamaha is an excellent sad after all these years of playing it. It’s easier to play and had a more comfortable thumb rest. And the original mouthpiece that came with it still produces a sound equal to my newer Yamaha 4C mouthpiece. Anyone looking for a good student model should check out the Yamaha YAS-23 Alto…
April 25, 2020 @ 4:01 am
Dear,a great list of musical instrument is available at China,you can visit the online store at:http://www.aliexpress.com/store/5784177