How Woodwind Pro Mike Livingston Built an Instrument Repair Business from the Road
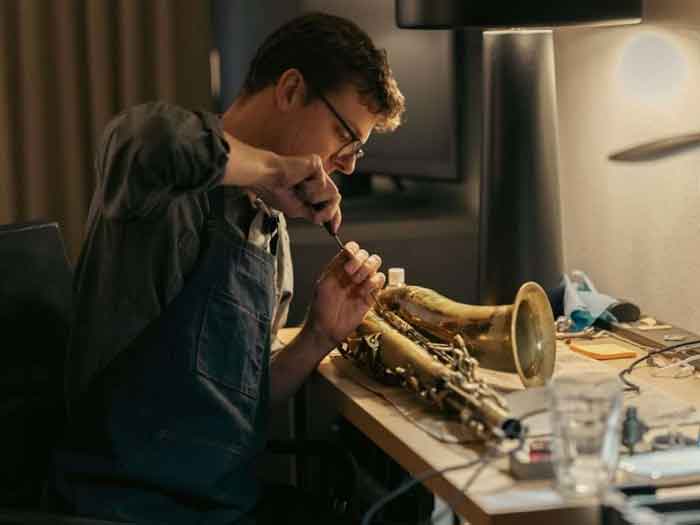
Introduction
Depending on where you live in the U.S, a good repair tech can be hard to find. Most cities don’t have the demand to support a saxophone specialist.
If you’ve struggled with this lack of instrument repair options, you might keep an eye on your local theater’s event schedule for Disney’s Frozen the Musical. as you may be able to have your horn(s) rescued by Mike Livingston, the show’s touring oboe/clarinet/flute/sax player who also happens to be an ace saxophone repair tech from New York City.
If you’re not familiar with Mike, you may have seen his work if you have tried a KB Sax neck or have had your saxophone repaired at JL Woodwinds. I was fortunate enough to sit down with Mike and discuss his experience repairing saxophones as well as the the evolution of his touring repair shop business.
Interview
ZS: What event or person led you to becoming interested in repairing saxophones?
ML: I’ve always been interested in how the saxophone works. I have memories of being a kid in school band, my mind drifting off studying the mechanics of the horn. Every time I went into a repair shop, I was very curious – and think a lot of people can identify with that. It seems like magic when you hand your broken instrument to someone and when you get it back and it suddenly plays better.
There was a repair tech at my college who I asked about a career in repair. He kind of laughed it off and said “You will never make any money doing it, and instruments today are meant to be disposable. The time for the old school repairman/craftsman is gone.” This was very discouraging, but I believed him and put it in the back of my mind.
At the same time my professor, Tim McAllister, encouraged me to diversify my skill set. He stressed that building a career as a musician often requires versatility. Years later, musical theater ended up taking me on tour with one-nighters, and as you are exploring these small towns everyone sort of finds a hobby. I was always going to pawn shops and looking for instruments, and anytime there was a repair shop or music store I would go in and ask a ton of questions. Some people offered great advice on books to read and tools to buy. Many recommended attending repair school, and some recommended finding a master to apprentice with. I loved hearing everyone’s story. I learned that everyone had a different journey to land behind their bench.
I started buying tools and books and tearing apart horns on my own in hotel rooms while touring. When my own instruments would break I would try to find a shop, but they could never turn around an instrument very quickly enough. I started to trust myself and my skills on my own horns. I realized it’s not magic, it’s mechanics and problem solving, and I can fix my own instruments.
My wife and I decided to move to New York in 2015 to give the Broadway scene a try. I wanted to take this opportunity to work alongside a great technician. By chance, I lived about a mile from Kim Bock’s shop (KBSAX) and walked in one day and told him my story. As luck would have it, Kim was stretched pretty thin at that time balancing overhauls and beginning to produce the KB necks so he gave me a shot. We spent several weeks going through the fundamentals of overhauling horns before we started getting into building necks.
I had a blast making hundreds of necks for Kim. The whole time I was doing this, I found that I wanted to spend more time repairing horns instead of making necks. Every time I caught up with the neck list I would run to Kim and ask to work on horns. This taught me that repairing was really what was in my heart. When I booked the Frozen tour, I left KB Sax but decided to focus on clarinet overhauls and repads from the road. Then the pandemic hit and the tour shut down. I set up a bench at home and kept working on clarinets.
At this time I set up an Instagram account and was just taking pictures of what I was doing and interest started to grow. Everyone was home shedding but had the time to part with their horns for repair work. Repair demand actually started to sky-rocket.
During that period I collected many more tools and a large supply of pads and resonators. When the Frozen tour returned, I packed up my whole setup. Pretty quickly players found me on the road through Instagram. Derek, the SaxSpy, found out I was going to be in town so he was helping me with my social media and putting it out there that I have a mobile repair shop.
It seems pretty unorthodox to have a shop that moves around but sometimes I’ll be in a city and there will be quite a demand. The repairs have started to evolve into me doing full overhauls. If people know I am coming to their town they will mail it to me ahead of time so I can hand it to them finished when they arrive. It’s really interesting to see how the business has unfolded. I really enjoy it.
ZS: When you started, what area or repair did you find most challenging? Are there certain saxophone models/brands that you find challenging/easiest to work on?
ML: The challenge is one’s own level of perfectionism. Any of the skills that go into it, you can really nit pick and make everything 100% perfect which takes a lot of time and patience. Pro shops work to balance great results with efficiency but when you’re working on your own horns it’s really pleasant and methodical to make everything perfect. Some areas of endless perfectionism include making tone holes flat, key-fitting, and pad installation. 90% of saxophones out there don’t have flat tone holes, the keys are sloppy, and the pads aren’t sealing well – but the saxophone is a pretty easy instrument to squeeze through those things. On the other hand, when everything is dialed in perfectly it feels so much better. The challenge is knowing how far to take it and knowing when to walk away.
ZS: Have you seen saxophone repair work improve or diminish over the time you have been repairing?
ML: I don’t think that the skills are that difficult if you put the time in. I think where you start to see the variety is in how rushed a tech was. If you’re rushing through the job it can be tempting to skip little things. At the end of the day it’s hard to make a living repairing slowly and methodically all of the time so a balance is important. Experienced technicians excel at working efficiently without sacrificing quality.
ZS: For those interested in becoming a repair tech, and specifically saxophones, what resources can they leverage to see if this would be a good career move?
ML: Matt Stohrer is an amazing resource for repair. His YouTube channel is full of amazing videos. If watching his videos excites you, try looking through his website. For anyone considering repair as a career, just like any music career, versatility will set up anyone to be successful. There are some shops that are very successful but they are not just repairing instruments, they are selling horns and accessories, renting lesson studios, and spending hours marketing and creating content on social media. For most of us repairing is just one tiny piece of the career puzzle.
ZS: You mentioned you have been doing repairs on the road. What has been your experience thus far?
ML: It does vary and it depends on who is in the area as far as repair shops and customers themselves. Sometimes I come to a place and I have a pile of my own old horns that I was going to work on. I try to balance life and the fact that there is more to life than just playing gigs and fixing saxophones. I am fortunate enough that I don’t have to fix saxophones to pay my bills but I really like doing it and maybe one day in the near future I will open my own shop. What I would really like to do is learn the same skills I learned from Kim and John but take it to oboe, flute, and clarinet repair.
ZS: As a mobile repairman, what is most challenging about doing repairs on the road?
ML: There are challenges to not having a consistent bench. Having to pack everything into a road box every few weeks limits some of the things I can stock like tons of different resonators and pads. When I need to source parts I can order them, but that usually takes a week of waiting. I am also constantly buying the smallest amount of chemicals since liquids are so heavy to carry around and it’s not the most efficient way to purchase these supplies.
ZS: What repair services do you offer while you are traveling?
ML: I do hourly repairs – that could be quick fixes or some will take a couple hours and the customer will drop it off. For overhauls, some people were bringing me their horns in the beginning of a two or three-week stint. This made me uncomfortable because I wanted to make sure I had time to get their feedback and make any final adjustments. This has led to more customers shipping me their horns ahead of time so I can overhaul it and have it ready to go for final adjustment and approval. I also enjoy coaching repair over video chat. This started as my friends would call in a panic needing help with their horns. I offer this coaching service to anyone around the world. Some of these have turned into regular weekly repair lessons.
ZS: When it comes to repair tools, what tools are a must have?
ML: There are a few things that can really save a player on the gig. A leak light is an excellent diagnosing tool. In a pinch a wedge shape of cigarette paper can be used as a feeler gauge. Screwdrivers and a spring hook are always useful. When it comes to corks and felts that fall out it’s nice to have spare cork and felts and use contact cement to re-attach. Cross-lock tweezers are useful when you are trying to glue a felt or cork in the dark on a set break. Teflon tape is a life saver if a neck cork starts crumbling or the neck cork loosens or compresses, but it’s only a temporary fix. There always seems to be a use for razor blades. I have links on my website to tools for the player and hobbyist repair tech.
Mike’s Setup
Saxophones:
- Soprano: Yamaha YSS-875
- Alto: Keilwerth SX90R
- Tenor: Guardala DG500
Necks:
- Tenor: KB Bronze thin-walled Prototype
- Alto: KB alto prototype necks
Mouthpieces:
- Soprano – Selmer C**
- Alto – Meyer 7
- Tenor: Bob Ackerman – Reso Chamber model 7*
Ligatures:
- Soprano: Rovner Ligature
- Alto: Rovner ligature
- Tenor: Rovner ligature
Reeds:
- Soprano: Rigotti Blue Box
- Alto: Rigotti Blue Box
- Tenor: Rigotti Blue Box
Accessories:
- Blayman woodwind stands (Blayman Music)
Other Instruments:
- Flute: Yamaha 381
- Clarinet: Buffet R13
- English Horn: Fox 555
- Oboe: Fox 330
Find out more about Mike on his website here or via IG: @mikelivingston_repairs